Destructive weld testing is a method used to ensure the quality and strength of welds used to join metals. In the context of auto body repair, welding is a common method for joining metal parts together, such as when attaching a new panel or repairing a damaged section of the vehicle’s frame. To ensure that the repair is safe and durable, the quality of the welds must be verified.
Destructive testing, as the name suggests, involves testing a weld to the point of failure to determine the weld’s properties, such as its tensile strength, impact resistance, hardness, and ductility. The goal is to gain information about the weld’s performance under stresses similar to what it would experience during the life of the vehicle.
Here are some common types of destructive weld tests:
1. **Tensile Strength Test:** This test measures the force required to pull the weld apart. A sample weld is loaded in a tensile test machine until the weld breaks. The force required to break the weld gives an indication of its tensile strength.
2. **Bend Test:** In a bend test, the welded component is bent to see if cracks appear in the weld or the base metal at the bend location. It can show the ductility of the weld, which is how much a weld can bend or be deformed before it breaks.
3. **Nick Break Test:** This test is performed by placing a notch or “nick” in the weld and then breaking the weld. When the weld is broken, the fractured surface can be examined for defects such as slag inclusions, porosity, and lack of fusion.
4. **Macroetch Test:** A cross-sectional sample of a weld is polished and then etched with acid to reveal the weld’s internal structure. This allows for the inspection of weld penetration and detection of imperfections within the weld or heat-affected zones.
The Goliath Carts Destructive Weld Testing Station at Body & Paint Center

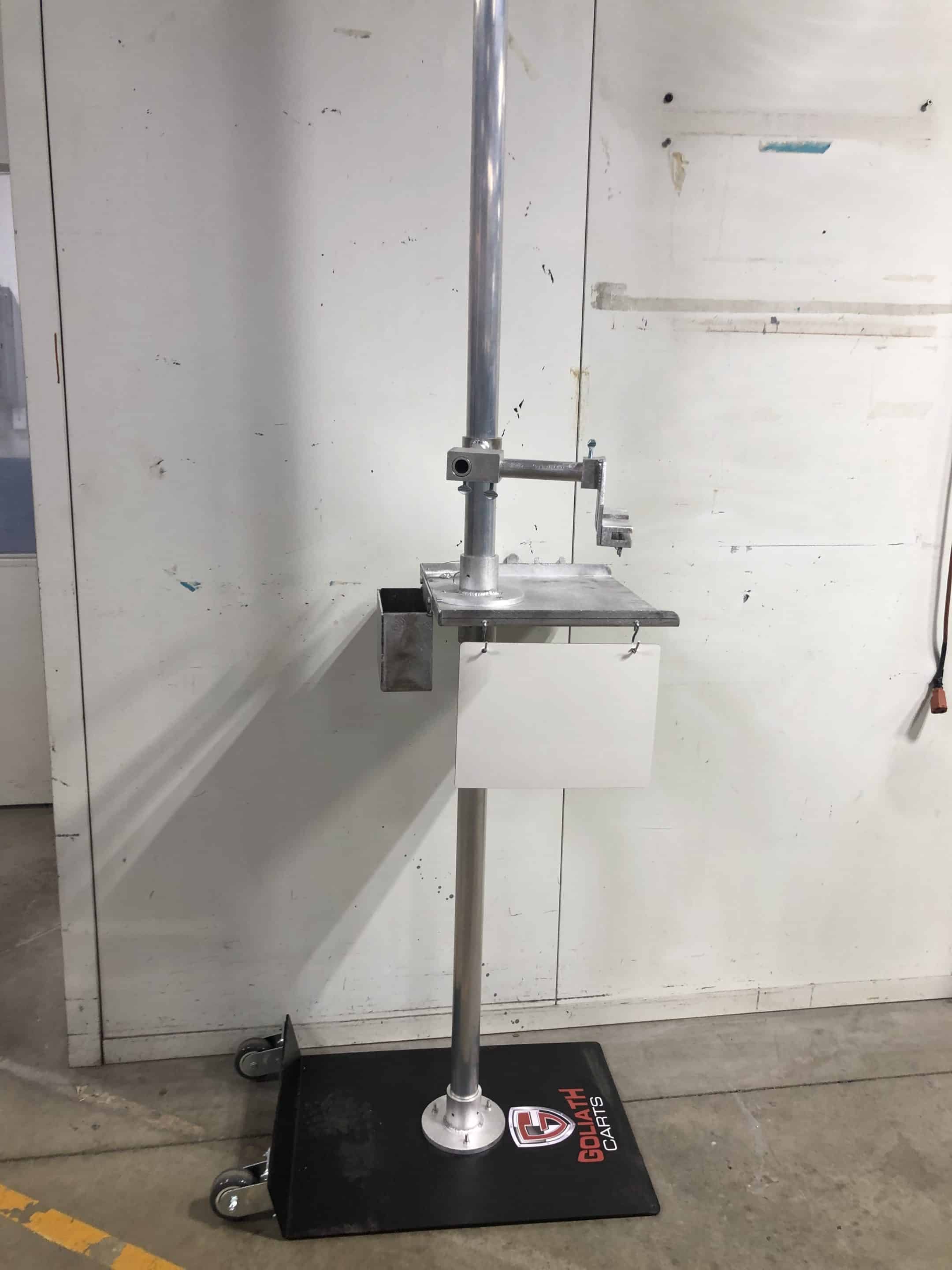
In auto body repair, the use of destructive testing can be practical during the training phase, where technicians learn to make proper welds, or when setting up a new welding process to ensure that the equipment is properly calibrated and that the procedures result in high-quality welds. Because these tests destroy the part being tested, they are not typically conducted on actual vehicles being repaired. Instead, test coupons (small representative pieces of welded material) are used to replicate the auto body’s material and thickness for testing.
If destructive testing indicates that a technician’s welds do not meet the necessary standards, the technician can adjust their technique or the welding equipment settings before performing actual repairs on vehicles. Ensuring the proper technique and settings can lead to safer and more reliable repairs and is part of maintaining quality control in an auto body shop.